DRYING
Drying of Textile Fabrics
Almost all type of natural, man-made, and artificial fibers, whether in loose or combed and spun form, or as continuous filaments, whether pure or blended, in any gauge or configuration, can be thoroughly dried to the desired residual moisture level with exceptional efficiency and superior outcomes. These exceptional results cannot be attained through any conventional hot air drying system. The radio frequency (RF) drying method for loose fibers subsequent to carbonization, bleaching, or dyeing, as well as batch or continuous centrifugal hydro extraction, offers numerous benefits.
These advantages include reduced product losses, consistent drying uniformity, enhanced physical-mechanical properties of the fibers, and consequently, more efficient processes for carding, combing, and spinning, resulting in a higher yarn metric yield of up to 2%. Tow slivers, in the form of pressed cakes, and tops slivers, dyed and hydro extracted as bobbins, bumps, or large forms after back-washing and roller squeezing, can all be dried while neatly folded on the conveyor belt of the "RF" series dryers.
This ensures a perfect distribution of residual moisture within the sliver and eliminates the lamination effects commonly observed in drum dryers. Hanks, after dyeing and centrifugal hydro extraction or inline squeezing, can be flawlessly dried without the need for movement or exposure to strong air currents, thereby preventing yarn entanglement, a typical issue encountered in hot air dryers, and significantly enhancing the efficiency of the winding process.
Prior to being placed directly onto the "RF" dryer conveyor belt, tops in bump and bobbin form can be dyed and centrifugally hydro extracted using mobile stainless steel basket-type carriers or directly on centrifugable spindles. Yarn packages, following dyeing, can undergo centrifugal hydro extraction or simply be pre-dried in a pressurized (rapid) dryer. Automated handling systems can be employed for the entire sequence of operations encompassing dyeing, hydro extraction, and drying.
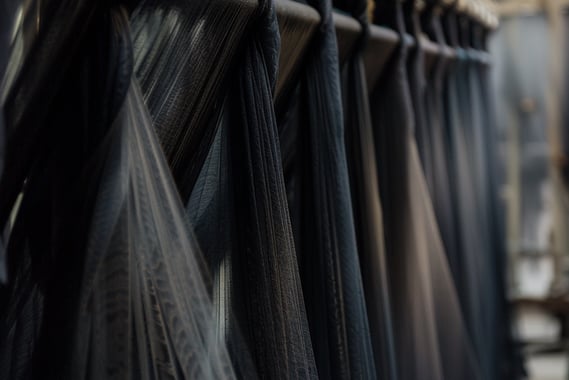
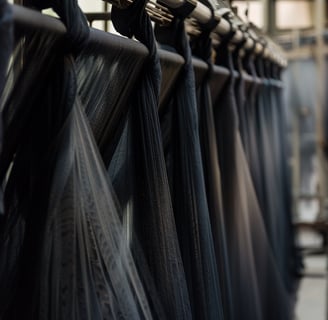
Common Materials
Cotton - Wool - Acrylic - Viscose - Linem - Silk - Nylon - Non-woven
Common Products
Fabrics - Yarn - Bump - Bobbin - Loose Fiber - Hosiery - Carpet - Moquette
Work frequency: 27,12 MHz Typical evaporation rates: 1.2 (H2O) kg/kWh Typical humidity rates IN/OUT: 30% - 2%
Drying of Insulating Materials
Work frequency: 27.12 MHz Typical evaporation rates: 1.1kg (H2O)/kW(RF)h Typical humidity rates IN/OUT: 15% - 0,1%
Bobbin - Insulating Panels - Catalytic Honeycomb - Powder
Glass Fiber - Rock Wool - Basalt Fiber - Wood - Foams - Ceramic - Silica - Polyamide
Common Materials
Common Products
In contrast, utilizing RF drying brings about a remarkable change. This advanced technique ensures that the drying process takes place uniformly throughout the entire product, both internally and externally. As a result, there is an avoidance of differential expansion and deformation, as the temperature and moisture levels are balanced, ensuring consistent quality across the entire material.
When it comes to insulating materials like foams or honeycomb ceramics, employing a conventional drying method poses challenges in effectively reaching the innermost layers of the product. In this case, the temperature distribution tends to be uneven, leading to varying rates of expansion that can adversely affect the overall quality.
Drying of Latex and Rubber
Pillow - Mattress - Glove - Condoms
Natural Latex - Latex in Molds - Latex layer in Continuous
Work frequency: 27.12 MHz Typical evaporation rates: 1.1 - 1.3 (H2O)kg/kWh (RF) Typical humidity rates IN/OUT: 30% - 1%
Common Materials
Common Products
Drying of Foam
RF drying operates independently of heat transfer mechanisms, ensuring rapid and efficient drying without the drawbacks of surface overheating or undesirable yellowing effects. It exhibits a remarkable selectivity towards water, swiftly absorbing RF energy and enabling rapid migration of moisture from the core to the surface. This eliminates any potential wet spots within the product, guaranteeing a uniformly dried outcome. Moreover, the energy delivered to the product can be precisely adjusted, allowing for meticulous control over both the evaporation rate and the residual moisture content.
The utilization of Radio Frequency (RF) drying presents a revolutionary approach that surpasses traditional heat-based methods. This innovative technique offers a multitude of benefits, especially when it comes to drying thick, shaped, and dense items such as casted blocks, mattress cores, and anatomic pillows.
RF machines can handle the entire drying process or seamlessly integrate with existing hot air dryers, such as tunnel or cabinet types, for partial drying. This synergistic combination enhances the production line's capacity and speed while maximizing energy efficiency and, most importantly, elevating the quality of the final product.
The advantages of RF drying are noteworthy. It achieves fast and uniform drying results, with a mere 20 minutes typically sufficient to dry even thick and dense mattress cores to below 1% residual moisture content, completely eliminating any presence of wet spots. Moreover, products with intricate shapes, such as pillows and anatomic seats, undergo perfectly uniform drying, whether in thicker or thinner sections.
An added advantage is that RF drying ensures the surface of the product remains free from yellowing, as the low temperature environment within the drying tunnel primarily heats the product's core rather than its external surface. This expedited drying process also reduces conditioning time, enabling swift packaging for shipment without the risk of molding during transportation to customers.
Furthermore, RF drying significantly reduces the footprint required for drying equipment due to its short process time. It operates with minimal noise, eliminates dust, fumes, and heat dispersion concerns, and offers instantaneous operation without the need for pre-heating. These features contribute to a highly efficient and environmentally friendly drying solution.
Work frequency: 27.12 MHz Typical evaporation rates: 1.1kg (H2O)/kW(RF)h Typical humidity rates IN/OUT: 15% - 0,1%
Common Materials
Common Products
Pillow - Mattresses - Panels - Sheets
SBR Foam - Polyurethane Foam
ADVANTAGES
Fast and uniform drying: about 20 minutes are sufficient to dry even thick and dense mattress cores below 1%.
residual moisture content, without any wet spots; also shaped products like pillows and anatomic seats dry perfectly uniformly in thicker parts as in thinner portions.
No yellowing of the product surface, due to low temperature in the drying tunnel (RF heats the product core, not its external surface).
Short conditioning time, so the product can be packaged for shipment quickly after drying without any risk of molding on the way to customers.
Significant reduction of drying equipment footprint, thanks to the short process time.
Little noise, no dust, no fumes, no heat dispersion.
Instantaneous operation(no pre-heating).